I tidernas begynnelse, 2008 för att vara mer exakt, var vi på ett litet studiebesök hos Coca-cola. Det var roligt och givande, men med tiden rann den relationen ut i sanden. Det var så klart tråkigt, särskilt eftersom vi hade samlat in frågor från våra läsare som vi aldrig lyckades få svar på. Kommunikation är svårt, och vår tid räcker inte (heller) alltid till.
Efter lanseringen av nya Fulcola i våras började vi försöka skapa och återuppta kontakten med de lokala tillverkarna, och Coca-cola var de som var lättast att nå fram till. Det är ganska naturligt att den största tillverkaren har mest resurser till PR och kommunikation, men man hade också kunnat tänka sig att de skulle vara minst intresserade av att prata med ett par enkla bloggare från webbens vildmark. Så var lyckligtvis inte fallet, utan de föreslog ett nytt besök för att ta en närmare titt på tillverkningen och ställa alla frågor vi ville. Vi var så klart inte sena att nappa på det erbjudandet, och efter lite mailande fram och tillbaka under våren hittade vi till slut en perfekt dag som passade alla inblandade.
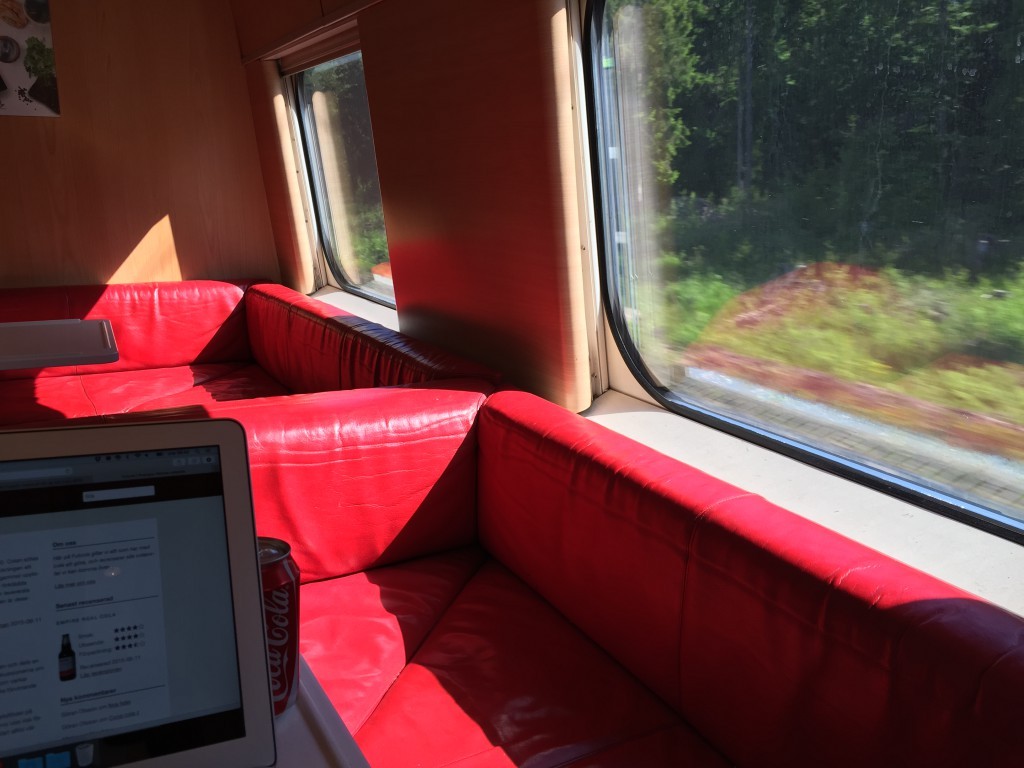
På spåret
Så, en solig dag i juni gick vi upp okristligt tidigt och hoppade på tåget mot Stockholm. I bagaget hade vi läsarfrågorna från förra omgången och en trave egna frågor som vi samlat på oss. Coca-colas svenska del sitter i Jordbro utanför Stockholm i en förvånansvärt stor anläggning med huvudkontor, tillverkning och lager. Egentligen finns det två olika företag bakom fasaden, The Coca-cola Company och Coca-cola Enterprises. De förstnämnda äger varumärkena, och de sistnämnda sköter produktion, distribution, försäljning och så vidare. Totalt jobbar ca 850 personer på anläggningen, vilket är mycket mer än vi hade väntat oss. Av dessa jobbar ungefär 150 personer med produktion, och på lagret hittas i runda slängar 200 personer. En rolig detalj är att 35 personer jobbar med att reparera och renovera kylskåp. Det kan låta lite märkligt, men Coca-cola har tusentals kylskåp i butiker och restauranger runt om i landet, och dessa behöver naturligtvis underhållas.
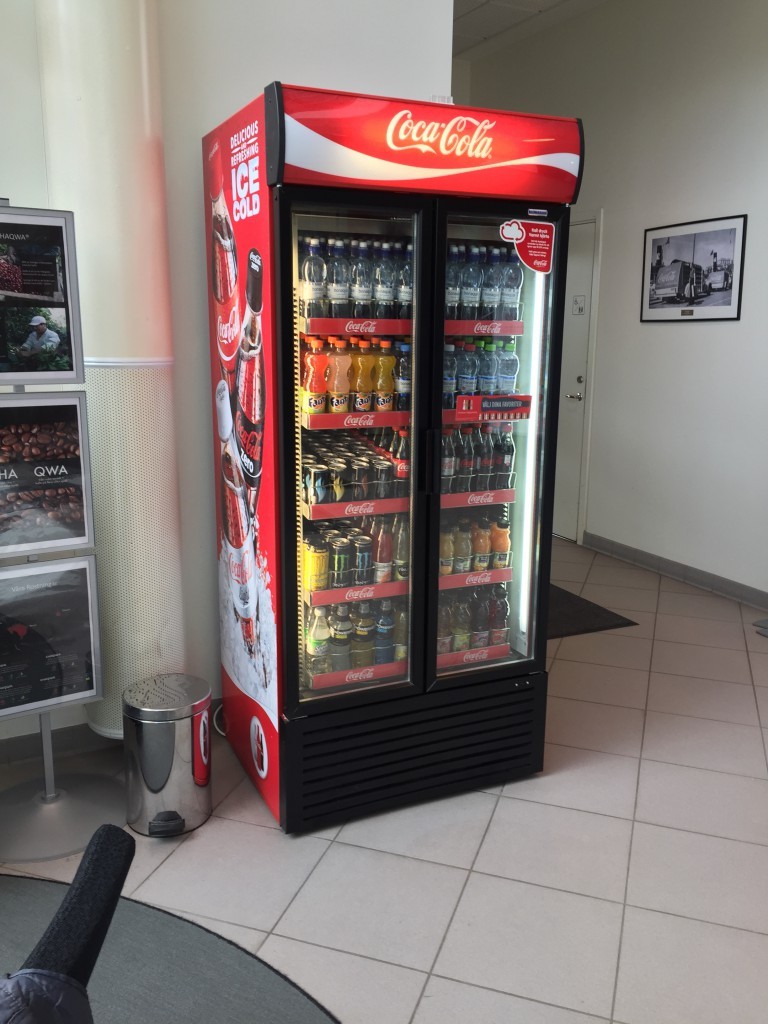
Hos Coca-cola är det föga förvånande god tillgång på just Coca-cola
Efter att ha kommit fram och ätit en välbehövlig lunch började vi vår rundtur. Första anhalten var en överblick av tillverkningen från en sorts lång balkong längs produktionslokalens väggar. Utöver de olika varianterna av Coca-cola produceras även exempelvis Fanta, Bonaqua och Mer i lokalerna, och dessa drycker tappas i förpackningar av olika typ och storlek.
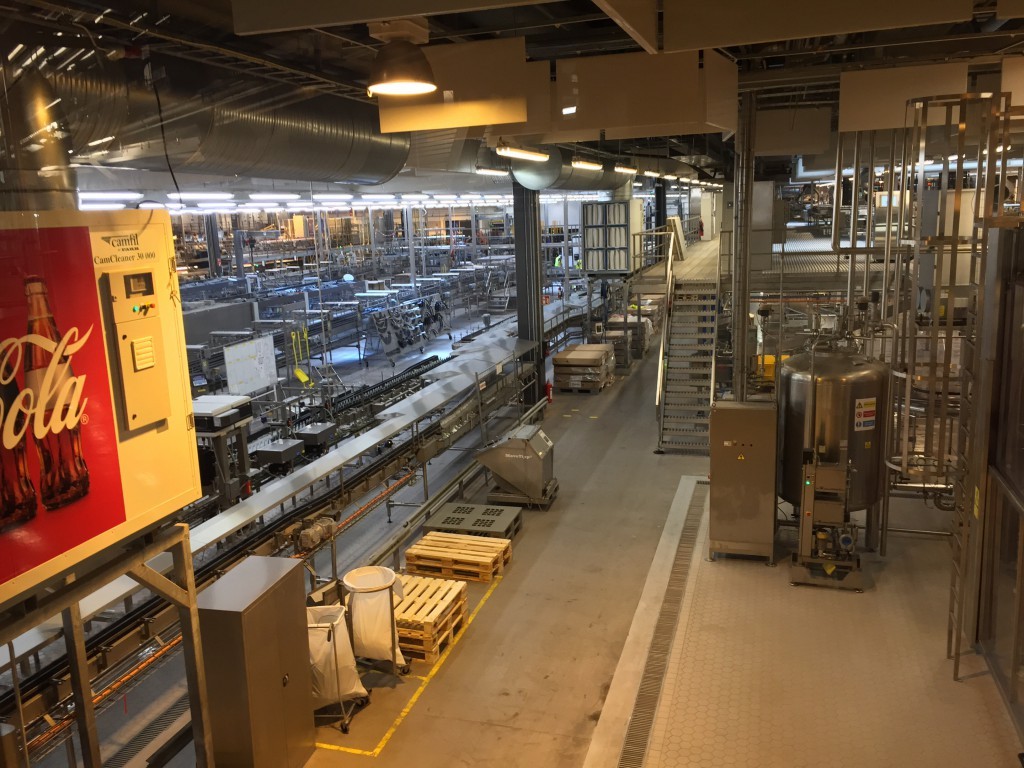
En liten del av Coca-colas produktionsanläggning
Coca-cola består i runda slängar av vatten, socker och det hemliga koncentratet som levereras från USA i två separata komponenter kallade A och B. De flesta är nog medvetna om att vattnet i colan hämtas från respektive land, men det är nog mindre känt att även sockret är lokalproducerat. Det är bra för oss i Sverige eftersom vi har finfina sockerbetor från Skåne, och slipper därmed den ofta fnysta åt majssirapen som används vid tillverkningen i USA. Där ses ofta cola med riktigt socker som något lite finare, men här finns det alltså att köpa i alla butiker hela tiden.
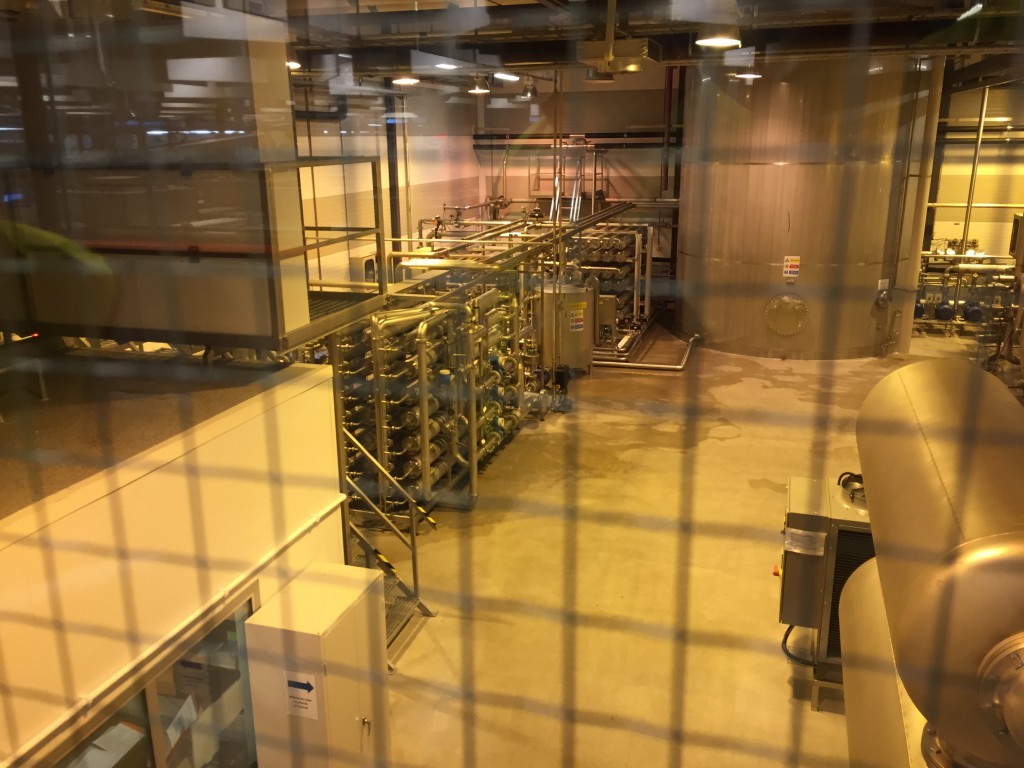
Vattenfiltreringsrummet, här filtreras kranvatten sju gånger innan det blir till Coca-cola
Vattnet kommer in i fabriken som vanligt kranvatten, och är redan då bland det renaste vattnet man kan hitta. Trots det filtreras det sedan hela sju gånger för att det ska hålla en så hög och jämn kvalitet som möjligt. Bonaqua är källvatten, som kommer in via en separat pipeline direkt från källan.
Själva tillverkningen av de olika dryckerna tar inte upp särskilt mycket yta vad vi kunde se, den absolut största delen av produktionsanläggningen sysslar istället med att fylla förpackningar, sätta etiketter på dem, bunta ihop dem på olika sätt och sedan lasta dem på pallar. En av anledningarna till att det tar upp ganska stor plats är att det krävs olika maskiner för olika typer av förpackningar. Maskinen som fyller glasflaskor kan exempelvis inte montera ihop aluminiumburkar, utan är helt fokuserad på just glasflaskorna.
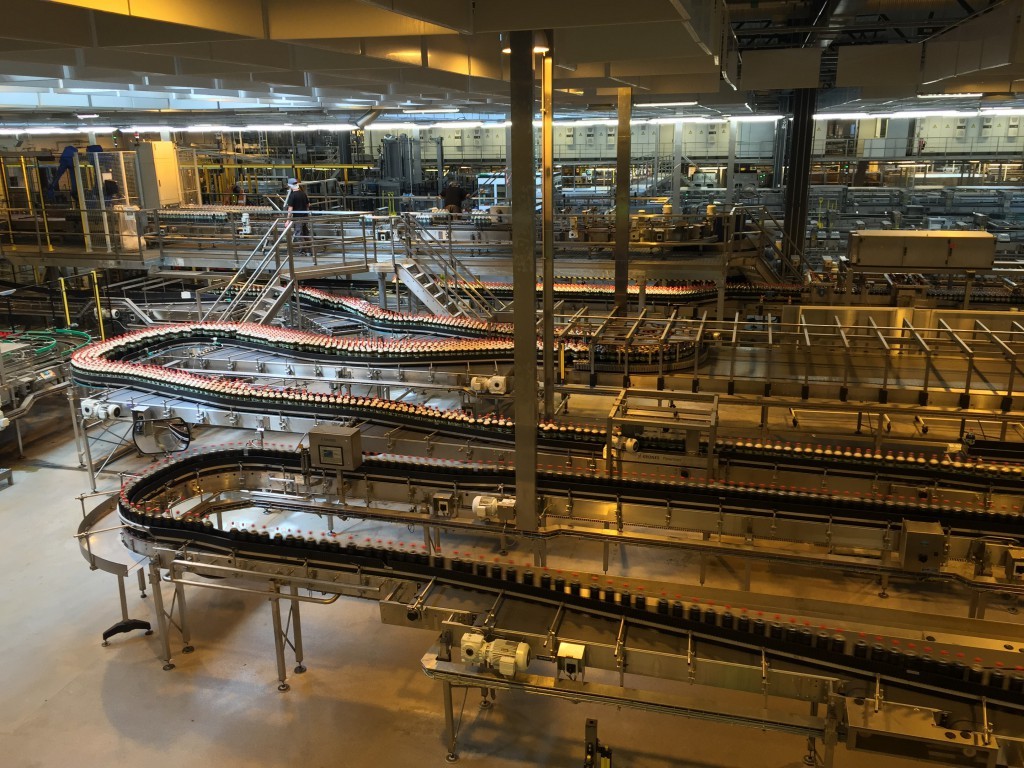
Mer utsikt över produktionen, där flaskorna åker åtskilliga hundra meter mellan de olika stationerna
I fabriken genomgår även vissa av förpackningarna de sista stegen i tillverkningen. PET-flaskorna levereras exempelvis i en sorts halvfabrikat som ser ut som små provrör, en liten flaskhals kan man säga. Dessa hettas upp till omkring hundra grader så att plasten blir formbar, och blåses sedan upp med tryckluft inne i en form för att få rätt tjocklek och utseende.
Efter översikten från balkongen fick vi klä på oss ytterligare skyddskläder för ett lite mer ovanligt besök ute på produktionsgolvet. Från det perspektivet kändes allt ännu större och mer komplext. Det finns förvånansvärt invecklade maskiner som gör till synes enkla arbetsuppgifter. Små robotarmar arbetade exempelvis flitigt med att vända var tredje Mer-tetra på ett löpande band ett halvt varv så att de kan plastas in som ett trepack på ett snyggt sätt. En maskin stor som ett par kylskåp fiskade upp PET-korkar från en behållare och såg till att de var vända åt rätt håll innan de skickades vidare för att skruvas på sina flaskor. Alla de här momenten imponerar så klart på oss som tekniknördar, man förstår att det ligger mycket arbete och kunnande bakom konstruktionen av såna här produktionslinjer. När allt fungerar ser det ut som en välkoreograferad balett, men det är rätt skönt att det är någon annans problem när det inte fungerar.
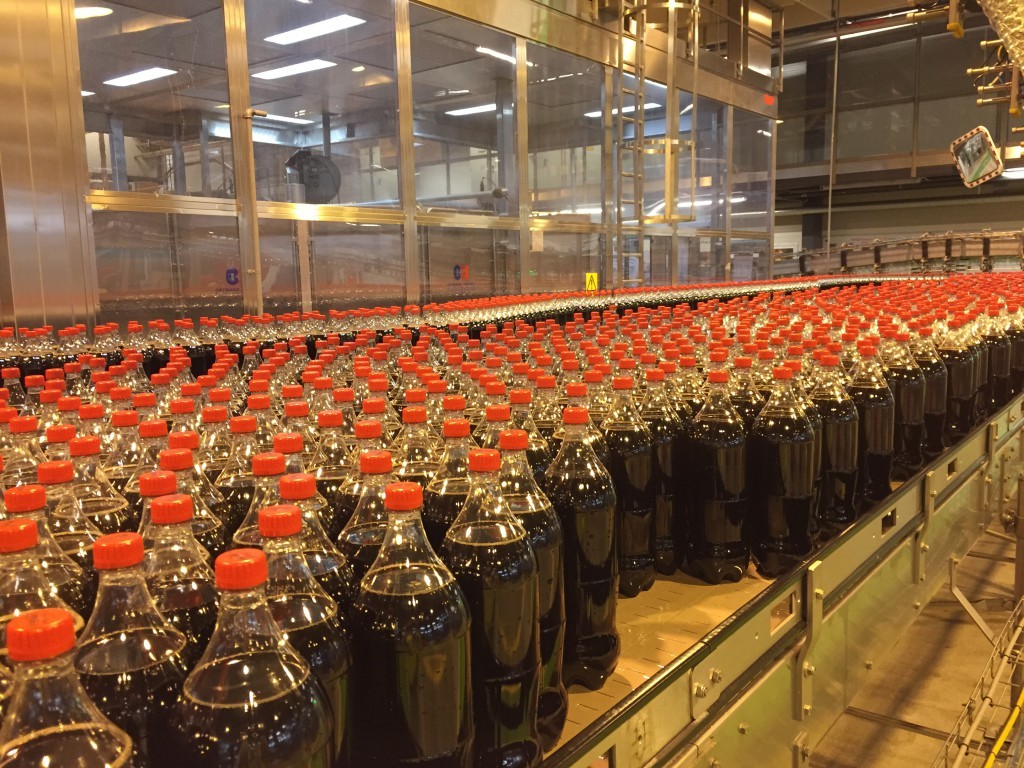
Flaskor på väg mot nästa steg i produktionen
Efter besöket i produktionen fick vi titta in i lagret, där produktionssiffrorna vi hade fått höra verkligen blev påtagliga. Fabriken producerar 400 miljoner liter dryck varje år, mer än en miljon liter om dagen alltså. Det gör man så klart inte i onödan, utan allt säljs och dricks i samma takt. På lagret finns ungefär tio dagars produktion, alltså över tio miljoner liter. Det är verkligen makalöst att stå och se det framför sig och tänka att var och en av alla miljonerna flaskor och burkar kommer att fraktas ut i butiker runt om i landet och säljas på en dryg vecka. Man häpnar!
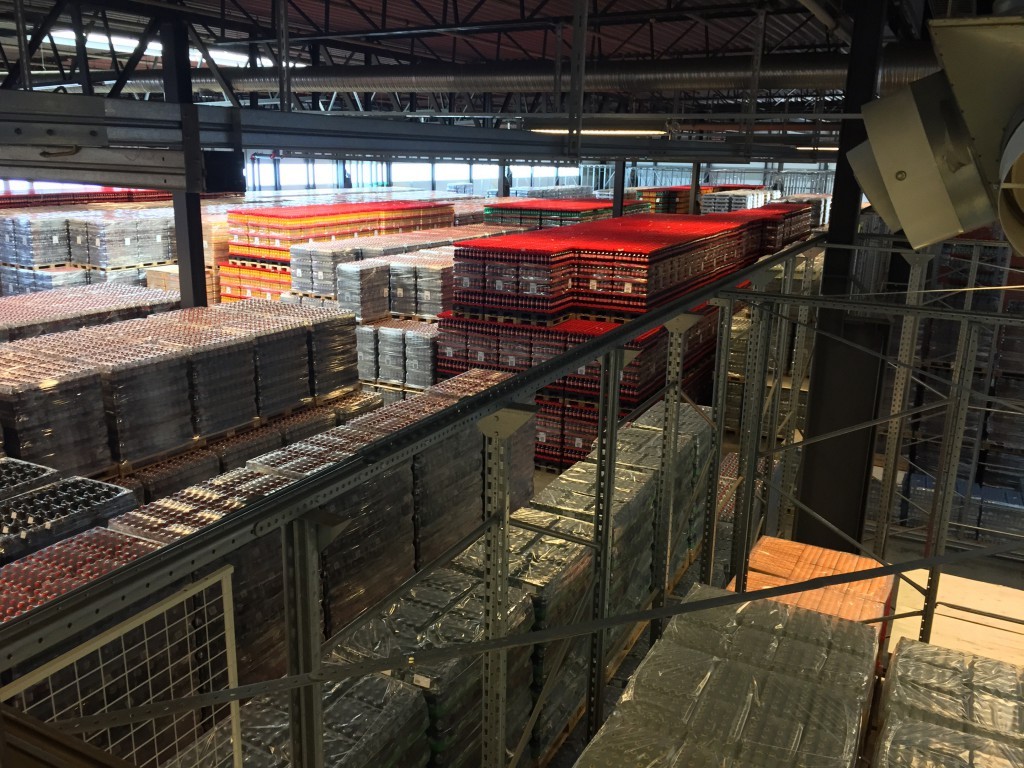
En liten del av Coca-colas lager, där tio dagars konsumtion alltid står redo väntar på att få levereras
Det var väldigt intressant att se hela produktionen på så nära håll, och faktiskt även att se de lite mer vanliga kontorsaktiga lokalerna. Man kan ha olika åsikter om både läsk och stora multinationella företag, men vi fick ett väldigt gott intryck av Coca-cola som arbetsplats. Alla verkade vara glada och ha det bra, och hälsade glatt när vi gick förbi både på fabriksgolvet och i korridorerna. Det skulle vara jättekul att besöka en mindre, eller till och med riktigt liten tillverkare som kontrast till den välsmorda industrin.
Efter rundvandringen satte vi oss ned för en uttömmande diskussion, den återkommer vi till i andra delen av den här lilla artikelserien.
ヽ( ゚ヮ・)ノ
Jag ser fram mot del två.
Vi filar på texten, men det går inte så fort såhär i semestertider :-)
Ser ju fram emot del två :D
Instämmer med Björn! :)
Jag vill se mer från erat besök!!!!!!!!!!!!!!!!!!!!!!!
Engagemanget värmer, vi håller på att bygga upp lite fart i Fulcola-maskineriet igen :-)